TA FLUX ROOT PROTECTION
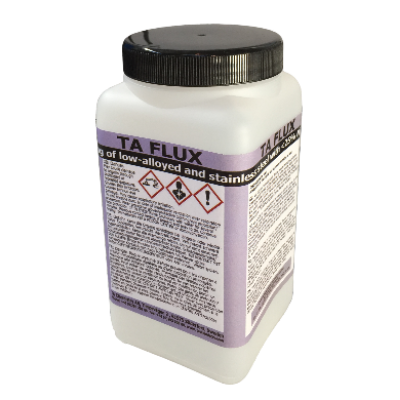
Testing (ASTM G48) revealed the following technical data:
- Loss of weight with argon-protection = 100%
- (100%=the loss of weight which occurs with argon-protection)
- Loss of weight with TA Flux = 180%
- (much better than without root-protection but not as good as argon-protection)
- Loss of weight without weld-protection = 318%
Contents: 500 g
Sold only in cartons (4 cans/carton)
TA Flux root-protector is delivered in powder form, which is mixed with denatured ethanol before welding. The distinguishing quality of the flux is its ability to eliminate oxide inclusions and the formation of tempering oxides during welding. The flux replaces protective gas (especially where the construction obstructs the use of protective gas on root side), tape and ceramic backing. The flux works also as weldsupport by distributing the heat evenly underneath the weld. Furthermore it acts chemically by effectively clensing the melt of contaminants. It is important to remove excess root flux and slag products after welding. This is best done with a stainless steel brush or grinding.
Areas of use:
Spot welding:
TA Flux is applied to the surfaces of the joint before assembling. It works as a clensing agent prevents the formation of tempering oxides in the vicinity of the spot welds. This process eliminates the risk of contaminating the weld joint and allows the spot weld to melt easily during the subsequent welding.
As a protective layer during welding:
TA Flux has several important functions when applied to the weld. The weld is protected against oxidation. The weld bead can be laid with a higher and constant speed. The flux’s moistening and supporting effects on the melt redirects the surplus heat from the local areas in the weld and thereby prevents uncontrolled penetrations and burn-through. Pin-holes are prevented by even, uniform heating and the absence of contaminants.
Overlapping welds:
TA Flux applied to the underside of overlaps prevents uncontrolled penetrations. Even heating and lower cooling speed prevents brittleness and gives stronger, more ductile welds.
Single-V-joints with different plate thickness:
TA Flux prevents burn-throughs when welding together thin and thick materials. Because the heat is evenly distributed local areas of high temperature are avoided and the welds penetrate uniformly.
Single-V-joints welded on one side:
TA Flux applied to the weld promotes even penetration with sufficient amount of material with initial bonding. Welds which previously needed welding from both sides can be effectively joined with a weld bead on one side.
Single-V-joints welded on both sides:
When joining thick plate, or where two-sided welding is necessary for quality’s sake, the flux should be applied to the weld before the first weld bead is laid. The even and strongly bound weld does not require chiselling or grinding. Brushing with a steel brush is recommended for removing slag remnants after the second weld bead.
Joining of low and high-alloy steel (composite steel):
When TA Flux is used the welder can bevel both the low-alloyed and the high-alloyed material prior to welding. This eliminates supplementary work with grinding and chiselling. When the flux is used with these alloys it should be applied to the high-alloyed side and welded beginning with the low-alloyed side.